Search products/applications
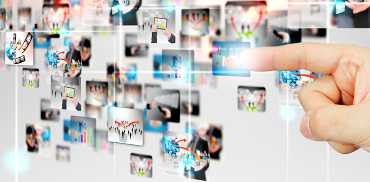
Search by
industories
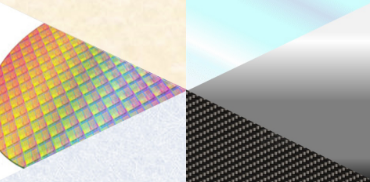
Search by
work materials
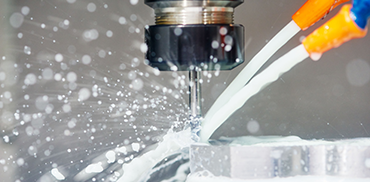
Search by
processing methods
News
- All
- Notice
- Event
- Media
- Other
- Column
-
2025.07.08 NoticeNotice of Summer Holidays
-
2025.04.29 Notice2025 Notice of GW vacation
-
2024.02.24 ColumnCase studies on wafer processing with diamond wheels in the semiconductor industry
-
2024.02.24 ColumnWhat are the Diamond Wheels? Useful basic knowledge for Diamond Wheels
-
2024.02.24 ColumnHow to prevent chipping in grinding? Causes and improvements in chipping
-
2024.01.10 EventSEMICON Japan 2023 Exhibition Report
-
2023.06.28 EventThank you for your visiting to our booth at “SEMICON West 2023″ in San Francisco, CA
-
2018.11.15 EventWe will be holding a exhibition at “SEMICON Japan 2018″ in Tokyo
-
2017.02.15 EventWe will be holding a exhibition at “27th FINETECH JAPAN″ in Tokyo
-
2016.09.20 EventWe will be holding a exhibition at “NAGANO SUWA AREA INDUSTRIAL MESSE 2016″ in Nagano
No data
-
2024.02.24 ColumnCase studies on wafer processing with diamond wheels in the semiconductor industry
-
2024.02.24 ColumnWhat are the Diamond Wheels? Useful basic knowledge for Diamond Wheels
-
2024.02.24 ColumnHow to prevent chipping in grinding? Causes and improvements in chipping
-
2024.02.24 ColumnWhat are CBN wheels? Types and characteristics of CBN Wheels. Summary of machining examples
-
2024.02.24 ColumnExamples of grinding processes by machining center and types of mounted wheels
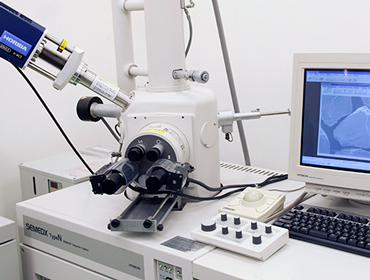
Technical information
You can find various basic information on diamond and CBN grinding tools, cutting tools, and other products, as well as technical information such as instruction manuals for major products to ensure the safe use of tools.
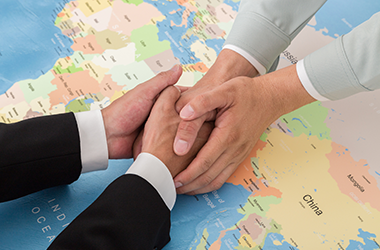
Supplier recruitment
Tokyo Diamond Tools Mfg. Co., Ltd. is looking for suppliers that can offer raw materials and new materials/processes to provide better products to our customers.
We are also looking for alliance partners with whom we can grow together and expand our business opportunities.