About diamond & cBN
Diamond is a mineral composed of carbon and is the hardest natural substance. In kanji it is written as "金剛石" (Kongoseki). The unit of quantity is carat (ct), which is the weight unit of gemstones. One carat is 0.2 grams.
In the latter half of the 20th century, synthetic diamonds were produced, and many of the diamonds used for industrial purposes today are synthetic. We offer tools that use synthetic and natural diamonds making use of the each characteristic.
In the machining of metal materials, especially iron-based materials, the carbon of diamond diffuses and permeates the iron structure in the material, and diamond, which is supposed to be hard, wears out unexpectedly quickly. Therefore, diamond tools are not suitable for machining iron-based materials.
The next hardest material after diamond is cBN (an acronym for cubic Boron Nitride, written as "CBN" in product names), a compound that does not exist naturally. It is inferior to diamond in terms of hardness at room temperature, but since it does not contain carbon, it is suitable for processing iron-based materials. By using diamond and cBN differently depending on the material to be processed, it is possible to achieve machining that makes the most of their respective features.
About grinding process & tools
Grinding process
Grinding is a type of removal process in which a wheel composed of abrasive grains and binders is rotated at high speed, and each randomly arranged abrasive grain acts as a cutting edge to remove a very small amount of material from the surface of the work material.
Grinding tools that use diamond or cBN as the abrasive grain are called "super abrasive wheels."
Since a large number of hard and fine blades are used, high quality machining of hard materials can be achieved.
In the process of grinding, abrasive grains are generally worn away and fall off (in some cases due to the self-generated cutting edge effect), and chips (shavings of the work material) are discharged.
Grinding fluid removes the heat generated by machining to cool down the work material, reduces the heat generation by improving the lubrication between the grinding wheel and the work material, and promotes the discharging of chips.
Image of grinding process and wheel structure
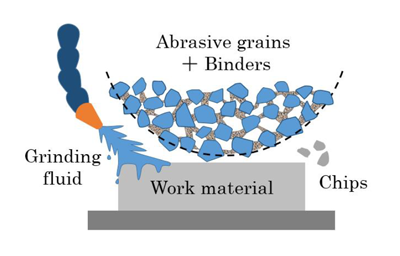
Types of grinding tools
There are two types of grinding tools depending on the position of the working surface of the abrasive grain layer: straight wheels (the working surface of the abrasive grain layer is on the periphery) and cup wheels (the working surface is on the end). In addition, there are the following types according to shape and application.
- Straight type: Centerless wheels (used on centerless machines), V-face wheels (with a V-shaped abrasive grain layer), multi-wheels (with several wheels combined), thread grinding wheels (with threaded outer circumference of wheels used on centerless machines), centering wheels (used for centering of lenses, etc.), ball grinding wheels (used for roughing of lenses, etc.)
- Cup type: 6A7S wheels (wheels with chips or pellets), double-headed wheels (a set of two wheels used in double-disc grinders)
- Deformed wheels (wheels with specially shaped abrasive grain layers, such as rounded or grooved abrasive grain layers): Beveling wheels (used for beveling semiconductor wafers and thin sheet glass), notching wheels (used for notching semiconductor wafers), etc.
- Cutting and grooving wheels: Rim saws, segment saws, multi saws, slicing saws
- Others: Small diameter mounted wheels, core drills
Types of grinding methods
-
Cylindrical grinding
This is the machining in which a cylindrical grinding machine or universal grinding machine is used to grind the periphery of a cylindrical work material with a rotating wheel. Depending on the direction in which the grinding wheel grinds the work material, there are two types of grinding: plunge grinding (grinding while moving the wheel or work material in the radial direction of the wheel) and traverse grinding (grinding while moving the wheel parallel to the work material's axial direction).
Depending on the relationship between the direction of rotation of the grinding wheel and the direction of movement of the work material, the cylindrical grinding can be classified as up-cutting and down-cutting.
Up-cutting: A grinding method in which the direction of rotation of the grinding wheel and the direction of movement of the workpiece are the same. The contact area between the grinding wheel and the work material is large, and efficient machining can be performed. Since the load on the grinding wheel is large and grinding resistance is also large, wear and tear is relatively large. It is a method of machining in which the chips are scooped upward from the bottom while being ejected outward.
Down-cutting: A grinding method in which the direction of rotation of the grinding wheel and the direction of movement of the work material are reversed. When the grinding wheel cuts the work material, it moves as if it is digging into the material while wrapping the chips inward. -
Internal grinding
A grinding method in which an internal grinding machine is used to grind the internal surface of a cylindrical work material with a rotating wheel. There are two types of internal grinding: the workpiece-rotating type, in which the work material is rotated to be processed while the grinding wheel is fed rotating, and the planetary type, in which the work material is fixed and the grinding wheel is fed while rotating and orbiting.
The planetary grinding method is suitable for machining heavy or complex-shaped work materials. Similar to cylindrical grinding, there are also traverse grinding and plunge grinding. -
Centerless grinding
A centerless grinding machine is used. In this machining, the periphery of a rotating cylindrical work material is ground using three parts: a fixed blade (support blade), a grinding wheel, and a rotating regulating wheel, without drilling a center hole in the work material.
Since the work material is not held or fixed in place by a chuck or other device, there is no mounting or dismounting process, which results in higher productivity.Through-feed grinding is a grinding method in which the grinding wheel and the regulating wheel are spaced at regular intervals and the work material is passed between them, making it suitable for mass production processing. The regulating wheel is slightly tilted and the rotated work material is fed axially.
Other types of grinding include in-feed grinding, end-feed grinding, and tangential grinding. -
Plane grinding
Using a plane grinder, the work material fixed on the table is pressed against a wheel rotating at high speed, and the surface is machined little by little. This process is used to adjust the thickness of the work material or to improve its flatness.
There are various grinding methods depending on the combination of the direction of the grinding wheel axis (vertical/horizontal axis) and the table shape (square table/circular table).Profile grinding (copy grinding, projection grinding)
A grinding method in which the shape of the product is enlarged and a projection drawing called a chart is drawn, projected optically onto a projector. The work material and chart are superimposed and the part that protrudes from the chart is removed.
This method is employed for the machining of tapers, groove widths, groove depths, convex radius, concave radius, etc. that require high precision. -
Gear grinding
A method of grinding and shaping the tooth surface of gears and other components using a gear grinding machine.
Screw grinding
A grinding method that uses a thread grinder to form threads.
-
Tool grinding
A grinding method that uses a specific grinding machine depending on the type of tool to be machined. It includes the following tool grinding machines: Drill grinder, hob grinder, front slice grinder, ultra-hard carbide grinder, broach grinder, shaving cutter grinder, saw blade grinder.
Identification system for wheels
Identification example
-
SDC
Abrasive
type -
200
Abrasive
size -
N
Binding
degree -
100
Abrasive
concentration -
BDH
Bond
type -
3.0
Abrasive layer
thickness (mm)
Abrasive type
Indication | Abrasive type |
---|---|
D | Natural diamond |
SD | Synthetic diamond |
SDC | Synthetic diamond with metal coating |
BN(cBN) | Cubic boron nitride |
BNC(CBNC) | Cubic boron nitride with metal coating |
A selection of abrasive grains for each material
Abrasive grains | Work materials |
---|---|
Diamond | Used for hard brittle materials such as glass, ceramics, silicon, ferrites, cemented carbide, quartz, and rock materials |
cBN | Used for nickel alloys, and heat-resistant alloys, and hardened steels |
Abrasive size
Abrasive size class | Size indication | Mesh size | Average size* (μm) |
---|---|---|---|
Mesh size | 60 | #60/#80 | 250 |
80 | #80/#100 | 177 | |
100 | #100/#120 | 149 | |
120 | #120/#140 | 125 | |
140 | #140/#170 | 105 | |
170 | #170/#200 | 88 | |
200 | #200/#230 | 74 | |
230 | #230/#270 | 62 | |
270 | #270/#325 | 53 | |
325 | #325/#400 | 44 | |
Micron size | 400 | 37 | |
600 | 30 | ||
800 | 20 | ||
1000 | 15 | ||
1200 | 13 | ||
1500 | 10 | ||
2000 | 8 |
* How to calculate (rough estimate of) average abrasive diameter D(average abrasive diameter μm) = 15000/(abrasive size)
Binding degree
Indication | Bond hardness |
---|---|
A | Softer |
~ | |
N | Standard |
~ | |
Z | Harder |
Abrasive concentration
Indication | Volume fraction(vol%) |
---|---|
200 | 50.0% |
175 | 43.8% |
150 | 37.5% |
125 | 31.3% |
100 | 25.0% |
75 | 18.8% |
50 | 12.5% |
The indication of concentration is set to 100, which corresponds to the volume fraction of 25%(vol%). (Approx. 4.4ct/㎝³ in case of diamond grain * 1ct(carat)=0.2g)
Types & characteristics of bonds
-
Metal bond
- Bonds that are powder sintered together with metal powders under strict temperature and atmosphere control.
- Excellent heat dissipation, high retention of abrasive grains, and excellent wear resistance.
- Metal bond can be used to produce form-grinding wheels that enable highly precise shaping using our unique machining technology and has high shape retention performance. -
Resin bond
- Thermosetting resin is the main component of this bond, and various fillers are available to meet a wide range of demands.
- Excellent sharpness and high-quality machining of mirror surface and others.
- Capable of producing complex shaped form-grinding wheels. -
Vitrified bond
- A bond with glassy inorganic material, available in porous and non-porous types.
- Excellent sharpness and self-sharpening under high load conditions by taking advantage of its hard and brittle properties.
- High flexibility in controlling the concentration of abrasive grains and porosity. -
Electroplated
- With a unique plating method, electrodeposition adheres abrasive grains with nickel plating.
- Overwhelmingly higher abrasive grain density compared to sintered bond wheels.
- The amount of protruding abrasive grains can be controlled, resulting in sharp and efficient grinding.
- Strong retention of abrasive grains with little dropout.
- Capable of manufacturing form-grinding wheels that can be used with various types of base metal. -
Reference of bond selection
Overview of wheel shapes
-
Wheel shape example breakdown (In case of 6A2C)
-
Standard base metal shapes
-
Abrasive layer shape cross sections
-
Abrasive layer position
-
Modifications
-
Designator of standard wheel shapes (Cup type)
Designator Wheel shape 6A2 Plan cup
6A9 Corner cup
9A3 Dual-sided cup
4A2 Dish
4C9 Dish
11A2 Flair cup
11V9 Flair cup (Corner with angle)
11C9 Flair cup (L-shape)
Designator Wheel shape 11Y9 Flair cup (L-shape with angle)
11B2 Flair cup (with angle)
12A2 Dish
12V9 Dish (Corner with angle)
12C9 Dish (L-shape)
12V4 Dish (inward slant)
12V5 Dish (outward slant)
-
Designator of standard wheel shapes
(Straight type)Designator Wheel shape 1A1 Straight
3A1 Straight with single-side boss
14A1 Straight with dual-side boss
6A1 Straight
9U1 U-shaped straight
1L1 Straight with chip breaker
Designator Wheel shape 1FF1 Straight with R
1F1 Straight with R
1V1 Straight with angle
1B1 Straight with angle
1EE1 V face
1E1 V face
About truing & dressing
What is truing & dressing ?
Truing is the process of removing runout and correcting the shape of the wheel's surface.
Dressing is the process of removing clogged or crushed grinding wheel surfaces to produce new sharp cutting edges or adjust the amount of protrusion of the new edge, which is essential for effective grinding.
It is necessary to select a truing/dressing method that is appropriate for the conditions of the tool, such as clogging, crushing, or spilling, and to select dressing conditions that are appropriate for the machining accuracy of the work material.